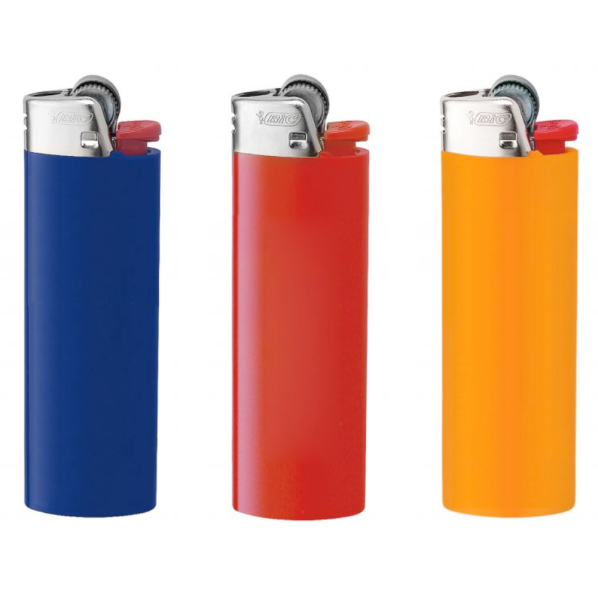
On-line logo visualisation
The logo visualization is not linked to the ordering process. For printed promotional products, please configure the product accordingly in the right column and upload the logo in the shopping cart.
More information about configuring a product can be found here.
BIC® Maxi (J26) Lighter
The delivery time depends heavily on the quantity ordered and is valid from the time of printing approval.
The average delivery time is:
Printing: about 10-15 working days
Delivery to Switzerland: about 4 working days
QC and delivery: about 2-3 working days.
Pad printing
Pad printing is an indirect gravure printing process in which the ink is transferred from the printing form to the substrate by an elastic pad made of silicone rubber. The ink is transferred to the material by pressing against it in different thicknesses. The advantage of this print transfer is the deformability of the pad, which makes it possible to print on curved surfaces. The printed image is transferred to the printing body. Due to the silicone oil in the pad, ink transfer to the substrate is almost 100%. In addition, a wide range of sizes can be printed in a wide range of colors. In the pad printing process, full colors can be printed according to PANTONE or HKS.
Screen printing
Screen printing is a printing process in which the ink is printed through a fine mesh fabric onto the material to be printed using a rubber squeegee. At those points of the fabric where no ink is to be printed according to the printed image, the mesh openings of the fabric are made impermeable to ink by a stencil. The advantage of screen printing is that the ink application can be varied by using different mesh finenesses, so that high ink layer thicknesses can be achieved. Compared to other printing processes, however, the printing speed is relatively low. Screen printing is mainly used in advertising and lettering, textile and ceramic printing, and industrial applications. Screen printing can be used to print solid colors according to PANTONE or HKS.
Digital printing
Digital printing refers to a group of printing processes in which the printed image is transferred directly from a file or data stream from a computer to a printing press without using a static printing form. Digital printing complements classic printing processes such as offset, gravure, flexographic or screen printing in all their areas of application where it would no longer be economical to print the desired low run lengths down to one-offs, and its dynamic print image generation opens up the possibility of various types of customizing. The digital printing process also makes it easy to print images on products.
Transfer printing
Transfer printing refers to a printing process in which the dye is transferred to a substrate. Transfer papers and foils as well as dyes or special inks are used for this purpose. The ink is then transferred to the product to be printed by means of the transfer foil. First, a special foil is printed with suitable dyes (side-inverted) and then transferred to the substrate using a press in the transfer printing process. The main advantages of transfer printing are that different materials can be printed in photo quality, the comparatively low costs and better environmental compatibility. Binding agents and solvents, which can be present in the fiber in other printing processes and would have to be washed out, can be dispensed with. In addition, the print is highly resistant to UV radiation and other environmental influences.